Digital Twins and Predictive Maintenance: Transforming Maritime Operations
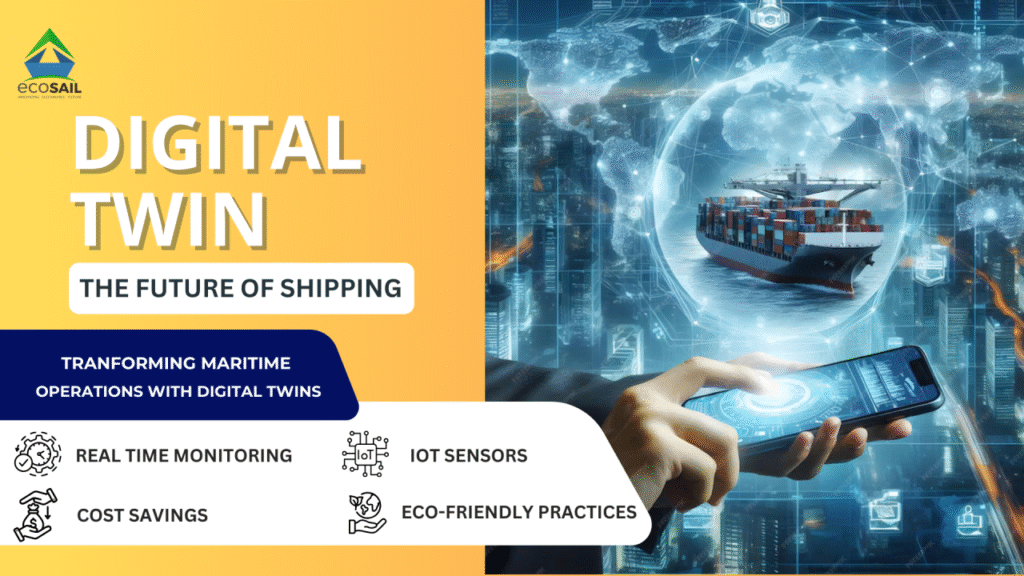
Digital Twins and Predictive Maintenance: Transforming Maritime Operations
The maritime industry is on the cusp of a digital revolution, with new technologies reshaping operations, enhancing sustainability, and driving efficiency. At the forefront of this transformation is digital twin technology, a powerful innovation that leverages real-time data, IoT, artificial intelligence, and cloud computing to create virtual replicas of ships and their systems. These digital counterparts enable shipping companies to monitor, simulate, and optimize vessel performance like never before. Among the most groundbreaking applications of digital twins is predictive maintenance, which allows operators to anticipate and prevent mechanical failures before they disrupt operations. Together, these advancements are not only enhancing operational reliability but also significantly contributing to environmental and economic sustainability.
Understanding Digital Twins in the Maritime Industry Digital twins are dynamic, virtual models of physical objects or systems that continuously receive data from sensors embedded in their real-world counterparts. In the context of maritime operations, digital twins replicate various components of a ship—including the engine, propulsion systems, fuel systems, and structural integrity. These models evolve in real-time as they ingest and process live data, offering a comprehensive and up-to-date representation of a vessel’s performance and condition.
The adoption of digital twin technology in the shipping industry represents a significant leap forward in maritime digitalization. Traditionally, ship maintenance and performance monitoring were based on scheduled inspections, manual logs, and reactive repairs. Digital twins transform this paradigm by enabling continuous, proactive monitoring of ship systems. Operators can visualize the vessel’s current status, simulate different operational scenarios, and identify inefficiencies or potential problems before they escalate.
The Driving Technologies Behind Digital Twins
The effectiveness of digital twins hinges on several interconnected technologies, each playing a vital role in enabling real-time insights and predictive capabilities:
1.IoT Sensors: Ships are increasingly equipped with Internet of Things (IoT) devices that collect data from various components. These sensors monitor temperature, pressure, vibration, fuel usage, speed, and numerous other parameters. The data gathered forms the foundation of the digital twin, enabling a high-fidelity, real-time replica of the vessel.
2. AI-Powered Predictive Maintenance Algorithms: Artificial intelligence and machine learning algorithms analyze the sensor data to detect patterns and anomalies. By comparing real-time data to historical benchmarks, AI can identify subtle signs of wear or degradation that may not be apparent through manual inspection. Predictive algorithms then forecast when and where a failure might occur, allowing for timely intervention.
3. Cloud Computing Platforms: Cloud-based infrastructure facilitates the seamless storage, analysis, and distribution of data collected from ships. It ensures that operators, whether onboard or onshore, have instant access to performance dashboards, maintenance alerts, and operational simulations. The scalability of cloud platforms also allows for fleet-wide monitoring and comparison.
4. Data Analytics and Visualization Tools: Advanced data analytics tools convert complex datasets into actionable insights. Visualization platforms, often using 3D modeling and augmented reality, help stakeholders understand vessel performance, maintenance needs, and optimization opportunities at a glance.
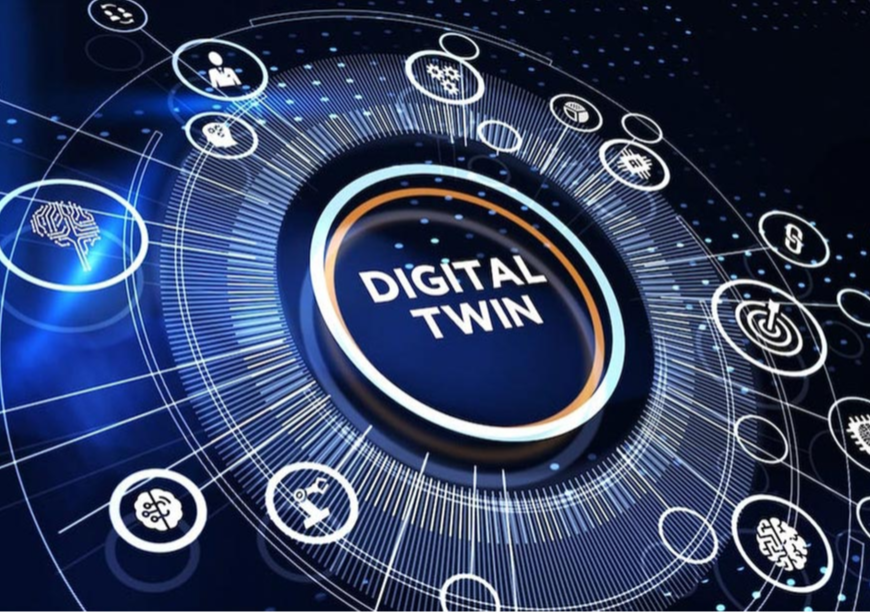
Predictive Maintenance
Anticipating Problems Before They Occur One of the most transformative aspects of digital twin technology is predictive maintenance. This approach marks a departure from traditional maintenance strategies, which often rely on fixed schedules or react to failures after they occur. Predictive maintenance enables shipping companies to shift from a reactive to a proactive maintenance culture.
By continuously monitoring the condition of machinery and systems, predictive maintenance algorithms can determine the remaining useful life of components and schedule maintenance activities accordingly. For example, if an engine pump starts to vibrate beyond normal levels or shows increased temperature, the system can flag this behavior, triggering a maintenance request before the pump fails entirely. This early detection prevents costly repairs, avoids downtime, and enhances crew safety.
Operational Benefits of Digital Twins and Predictive Maintenance The integration of digital twins and predictive maintenance offers a multitude of operational advantages:
- Increased Efficiency: Real-time monitoring and optimization of systems reduce fuel consumption, extend the lifespan of components, and minimize unnecessary repairs.
- Cost Savings: Predictive maintenance reduces the incidence of emergency repairs, minimizes unscheduled downtime, and allows for better resource allocation.
- Enhanced Safety: Continuous system diagnostics help identify safety-critical issues before they pose a threat to the crew or vessel.
- Improved Decision-Making: Access to real-time and historical performance data empowers operators and management to make informed, data-driven decisions.
- Fleet Management Optimization: Cloud-based digital twins allow for centralized fleet monitoring, enabling benchmarking across vessels and standardization of best practices.
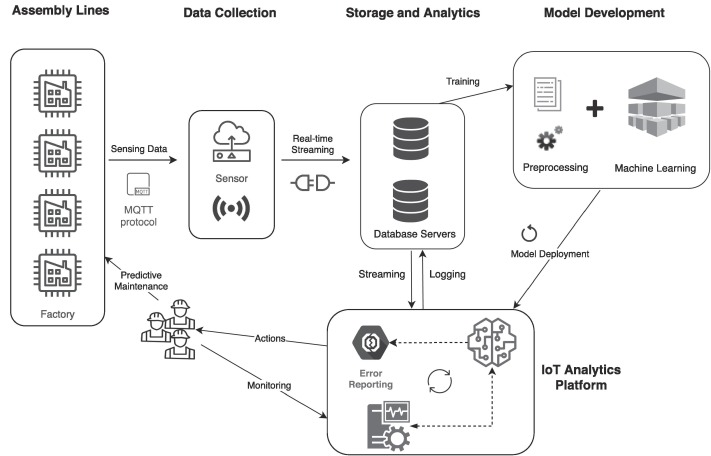
Driving Sustainability in Maritime Operations Beyond operational improvements, digital twins and predictive maintenance are vital tools for advancing sustainability in maritime transport. The shipping industry is under increasing pressure to reduce its environmental footprint, comply with stricter emissions regulations, and transition toward greener operations. Digital twins play a critical role in achieving these goals.
- Reduced Fuel Consumption and Emissions: By monitoring fuel efficiency and optimizing engine performance, digital twins help vessels consume less fuel and emit fewer greenhouse gases. Even marginal improvements in efficiency can lead to substantial environmental benefits when scaled across large fleets.
- Minimized Resource Waste: Predictive maintenance ensures that parts and components are used to their full potential before being replaced. This reduces material waste and the environmental impact associated with manufacturing and logistics.
- Lower Risk of Environmental Incidents: Early detection of equipment failures can prevent incidents such as oil leaks, exhaust malfunctions, or engine breakdowns that could harm the environment.
- Support for Carbon Reporting and Compliance: Detailed performance data from digital twins supports accurate carbon accounting and reporting, helping companies comply with IMO regulations and carbon intensity targets.
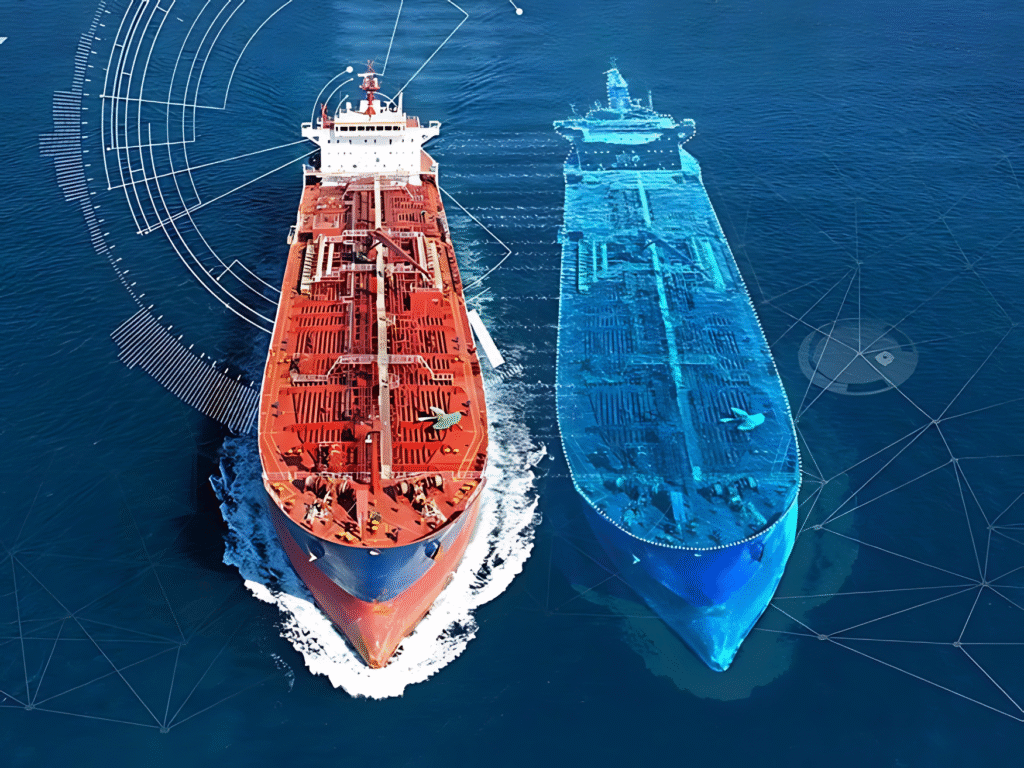
Case Studies and Real-World Applications Several leading maritime organizations have already embraced digital twin technology:
- Rolls-Royce Marine: Developed virtual ship models integrated with onboard sensors to monitor engine health and improve operational planning.
- Maersk: Has invested in digital twin platforms to enhance fleet performance and sustainability outcomes.
- Kongsberg Digital: Offers “Kognifai,” a digital twin ecosystem designed for remote vessel monitoring, energy management, and predictive analytics.
These implementations demonstrate that digital twins are no longer theoretical concepts but practical tools transforming modern maritime operations.
Challenges and Considerations While the benefits of digital twin technology are compelling, certain challenges must be addressed to ensure successful implementation:
- High Initial Investment: The cost of installing IoT sensors, developing digital models, and integrating cloud platforms can be significant.
- Data Management Complexity: Handling and securing vast amounts of operational data requires robust cybersecurity measures and data governance frameworks.
- Skill Gaps: Maritime personnel must be trained to interpret digital twin outputs and leverage predictive analytics effectively.
- Standardization Needs: Industry-wide standards for digital twin development, data formats, and integration protocols are still evolving.
Conclusion
The Future of Maritime Operations The integration of digital twin technology and predictive maintenance marks a pivotal shift in the way maritime operations are conducted. From improving ship reliability and reducing operational costs to enhancing environmental sustainability, the benefits are far-reaching. As digital twin platforms become more sophisticated and accessible, more shipping companies are expected to adopt these technologies as part of their digital transformation strategies.
Looking ahead, the maritime industry will likely see even greater convergence of digital twins with other innovations such as autonomous navigation, decarbonization strategies, and blockchain for supply chain transparency. By embracing these changes, the industry is charting a course toward a future that is smarter, safer, and more sustainable.